How to select a magnet
Although magnets are used widely around us, we do not get to directly see them often because they are usually used inside devices. Since we do not actually handle them often, many customers are not sure how to select a magnet. Please refer to the below information when selecting a magnet.
1Selecting a magnet based on the type of material
The major types of magnets are neodymium magnets, ferrite magnets, samarium cobalt magnets and alnico magnets. Each type has different characteristics. Please check the differences in properties in order to select a suitable magnet for your usage.
φ10mmX10mm | Magnet | Element symbol | Name of element | Advantages | Disadvantages | Usage |
---|---|---|---|---|---|---|
![]() |
Neodymium | NdFeB | Neodymium Iron Boron |
This is the strongest magnet that currently exists. It has high mechanical strength. Recently it is high in demand. We can make these magnets even in small lots | It rusts easily so must be surface treated. Usually it is nickel plated. The price of rare earthes, the raw material used, is soaring. | Hard disk, MRI, hybrid automobiles |
![]() |
Ferrite | Fe2O3 BaCO3 or SrCO3 |
Ferric oxide barium carbonate or strontium carbonate |
This low cost raw material is suitable for use in high volume production. Anisotropic ferrite is practical because it has relatively good adsorptive power. | It chips easily like china. Not suitable for prototypes in small lots because a metal mold may be necessary. | Speakers, monitors |
![]() |
Samarium cobalt | SmCo | Samarium Cobalt |
It has excellent coercivity and is suitable for use in high temperature environments. | It is brittle and chips easily. The price of rare earthes, the raw material, is soaring. | Motors |
![]() |
Alnico | AlNiCo | Aluminum Nickel Cobalt |
It has excellent mechanical strength and is suitable for use in high temperature environments. | Recently the demand is low and in most cases metal molds are required because they are manufactured through a casting process. It demagnetizes easily even when exposed to repelling magnetic fields. | Precision machines Horse shoe (U) shaped compass |
Rubber magnet sheets | CM | Chlorinated Polyethylene | It is made from a mixture of resin and ferrite magnet powder, is flexible and can easily be machined to your desired shape. | It is made from a mixture of resin and ferrite magnet powder, is flexible and can easily be machined to your desired shape. | Learner driver decals Protection for elevators etc |
2Selecting a magnet based on the size and shape
The properties of the magnet will differ greatly according to the size and shape (round, Rings, square, segmented). Take into consideration whether the magnet will fit in the object in which you wish to place it, whether the magnet is too thick or too thin, and then select the size which would be easiest to handle. For round neodymium magnets, we have a wide range of sizes from φ1mm to overφ100mm in diameter.
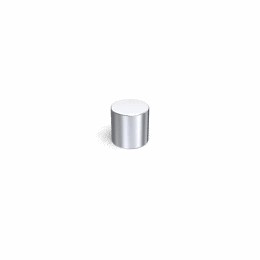
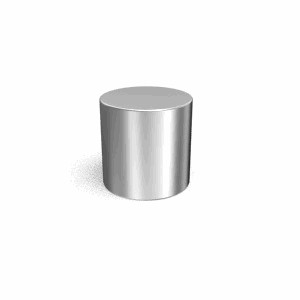
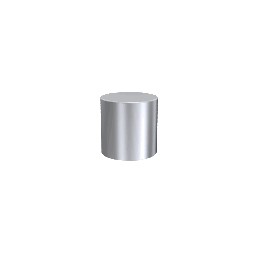
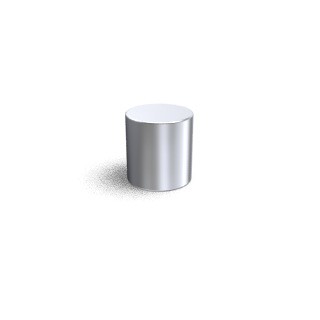
Neodymium magnets | φ1mmX1mm | φ2mmX2mm | φ5mmX5mm | φ10mmX10mm |
---|


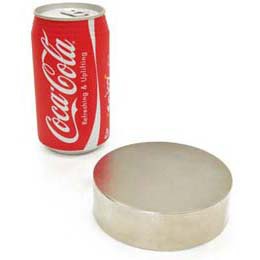
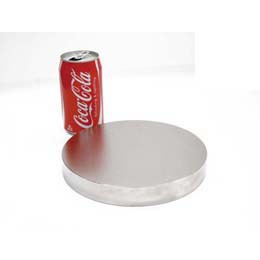
Neodymium magnets | φ15mmX15mm | φ20mmX20mm | φ100mmX30mm | φ195mmX27mm |
---|
3Selecting a magnet based on the adsorptive power
Adsorption power is the weight in kilograms(Kilogram-force 1 kgf = 9.80665 N)when the magnet is attached to an iron plate (thicker than the magnet itself) and pulled perpendicularly in the direction of magnetization. The property value shown as "Adsorptive power Kg" is the value when the property is utilized to its maximum. It is a reference value and not a guaranteed value. The adsorptive power (Kgf) is given in the list of sizes. Please use these values to help you select a suitable magnet.
Adsorptive power and magnetic flux density
The adsorptive power and magnetic flux density are not proportional to each other. The adsorptive power increases if the installation area is large.
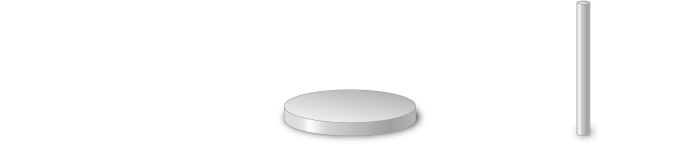
N35 | φ100mmX10mm | φ10mmX100mm |
---|---|---|
Magnetic flux density | 117mT | 546mT |
Adsorptive power | 50kg | 4.2kg |
4Selecting a magnet based on the magnetic flux density (gauss, millitesla)
The magnetic flux density (gauss, millitesla) is given in the list of sizes as a reference value. The magnetic flux density refers to the magnetic flux (number of lines of magnetic field) per unit area. The SI unit is called the tesla (T) and the CGS unit (Mx/cm2) is called the gauss (G).
The surface magnetic flux density, a property that is shown after machining and completion of the product, can be either a value measured by a device such as the gauss meter or a predicted value based on calculations. There is no set standard in the magnet industry for measuring surface magnetic flux density since the measuring devices, environmental conditions for measuring and calculation formulas differ according to the manufacturer.
Comparison of properties, categorized according to shape
The magnetic flux density and adsorptive power are not proportional to each other. The thicker (taller) the magnet in the direction of magnetization, the higher the magnetic flux density.
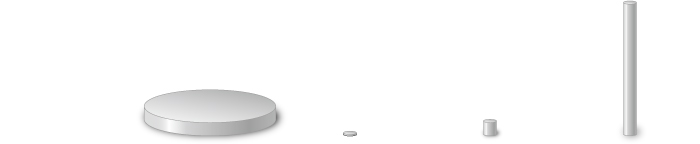
N35 | φ100mmX10mm | φ10mmX1mm | φ10mmX10mm | φ10mmX100mm |
---|---|---|---|---|
Magnetic flux density | 117mT | 113mT | 488mT | 546mT |
Adsorptive power | 50kg | 0.5kg | 3.4kg | 4.2kg |
Heat resistant 80℃ | 60℃ | 60℃ | 105℃ | 150℃ |
Property tendencies, categorized according to shape
The larger the maximum energy product, both the adsorptive power and magnetic flux density will be stronger.
Max energy product BH-max |
Installation surface area & adsorptive power Kgf | |||||
---|---|---|---|---|---|---|
Narrow | → | → | → | Wide | ||
Direction of magnetization Flux density Br Coercivity H |
Low & thin | 1 | 2 | 3 | 4 | 5 |
↓ | 2 | 3 | 4 | 5 | 6 | |
↓ | 3 | 4 | 5 | 6 | 4 | |
↓ | 4 | 5 | 6 | 7 | 8 | |
High & thick | 5 | 6 | 7 | 8 | 9 |
5Selecting a magnet based on temperature of usage environment
The magnetism of a magnet repeatedly changes from strong to weak and vice versa according to the environmental temperature. If the temperature rises by even just one degrees, the magnet weakens and if the temperature rises by one degrees it will become stronger. Therefore when choosing a magnet suitable for your environmental temperature, it helps to know the coercivity of the material. The temperature coefficient and maximum operating temperature can be calculated from the coercivity. The maximum operating temperature is referred to as the heat resistant temperature.
Usually the magnetism will completely return to its original state after cooling. However, it will become irreversible if the temperature exceeds the heat resistance temperature and the magnetism will not return to its original state even at normal temperature as the magnetism will have been lost in proportion to the amount that was exceeded. Remagnetizing a magnet with a reduction of magnetism due to heat can recover the magnetism to almost its original state. Also, the heat resistance temperature is not the Curie temperature at which the magnetism is lost totally. If the temperature exceeds the Curie temperature, the magnet will completely lose its magnetism and become just a plain stone.
Comparison of heat resistance due to heat permeability
The heat resistance will differ according to the shape of the magnet even if the material has the same properties because the heat permeability will differ according to the size (shape and thickness) of the magnet. The heat resistance will be higher if the magnet is thicker in the direction of magnetization and lower if it is thinner. The heat resistance temperature that is stated on the specification is a reference value and not a guaranteed value.

N35 | φ10mmX1mm | φ10mmX10mm |
---|---|---|
Heat resistant 80℃ | 60℃ | 105℃ |
Maximum tooling heat resistance temperature and Curie temperature
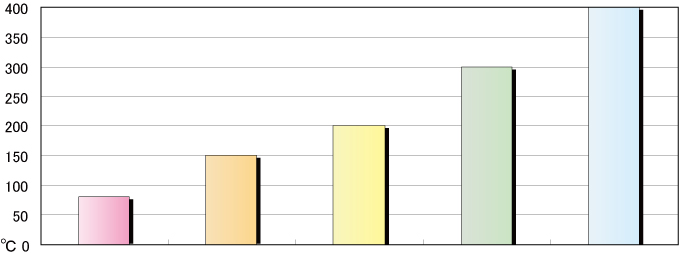
Properties | Neodymium | Heat-resistant neodymium | Samarium cobalt | Ferrite | Alnico |
---|---|---|---|---|---|
Maximum tooling heat resistance temperature | 80℃ | 150℃ | 200℃ | 300℃ | 400℃ |
Curie temperature | 310℃ | 340~400℃ | 710℃ | 450~460℃ | 850℃ |
Temperature coefficient Br/℃ |
±0.12% | ±0.09% | ±0.035% | - | - |
6Selecting a magnet based on rust resistance
Neodymium magnets rust easily so they are usually coated with nickel plating to prevent rust. However using them outdoors and close to water will still cause corrosion.
The best surface treatment for rust resistance is our epoxy Hi-DEN coating.
Anti-rust performance test Ni/Zu/Epoxy
Magfine | Company[S] | Other companies |
Magfine | Company[T] | Magfine | |
---|---|---|---|---|---|---|
Duration | HDCcoating epoxy MF304 |
Normal epoxy |
Anti-rust undercoat Zn for automobiles Zn |
HDC coating polyimide MF305 |
Normal epoxy |
NiCuNi |
Before start of test | ![]() |
|||||
After 72 hrs | ![]() |
|||||
After 312 hrs | ![]() |
|||||
After 504 hrs | ![]() |
Salt spray test:37-39℃ 5%NaCl PH6.5-7.0 1.5ml/Hr
PCT: 120℃, 2atm, 100%RH, 12Hr.
For details of Hi-DEN Coat click here
7Select by characteristics
Please select magnets with magnetic characteristics suitable for the operating environment.
Magnetic properties comparison
Material | Grade | Remanence | Coercivity | Coercivity | Maximum energy product |
Heat resistant temperature |
Curie temperature |
Temperature coefficient |
|||||
---|---|---|---|---|---|---|---|---|---|---|---|---|---|
αBr | αHcj | ||||||||||||
Br | Hcb | Hcj | (BH)maX | TW | TC | Br/℃ | Hcj/℃ | ||||||
mT | kG | kA/m | kOe | kA/m | kOe | kJ/m3 | MGOe | ℃(H/D=0.7) | ℃ | %℃ | %℃ | ||
Neodymium | 35 | 1170-1220 | 11.7-12.2 | 868 | 10.9 | 955 | 12 | 263-287 | 33-36 | 80℃ | 310℃ | -0.12 | -0.6 |
33AH | 1130-1170 | 11.3-11.7 | 843 | 10.6 | 2624 | 30 | 247-271 | 31-34 | 230℃ | 400℃ | -0.09 | -0.45 | |
Samarium cobalt |
YXG30H | 1080-1100 | 10.8-11.0 | 788-835 | 9.9-10.5 | 1990 | 25 | 220-240 | 28-30 | 350 | 800 | -0.035 | -0.20 |
YXG28 | 1030-1080 | 10.3-10.8 | 756-796 | 9.5-10.0 | 1433 | 18 | 207-220 | 26-28 | 300 | 800 | -0.035 | -0.20 | |
Ferrite | Y30H-1 | 380-400 | 3.8-4.0 | 230-275 | 2.87-3.44 | 235-290 | 2.94-3.62 | 27-32 | 3.4-4.0 | 200℃ | 450℃ | -0.18 | +0.2 |
Alnico | LNG40 | 12.5 | 1250 | 48 | 0.60 | - | - | 40 | 5.00 | 525 | 860 | -0.02 | +0.02 |
Physical properties comparison
Material | Grade | Specific heat |
Thermle xpansion coefficient |
Specific heat capacity |
Specific electrical resistance |
Density | FleXural strength |
Compr essive strength |
Tensile strength |
Young's strength |
Vickers hardness |
|
---|---|---|---|---|---|---|---|---|---|---|---|---|
1/℃ | μrec | cal/g・℃ | Ω・cm | g/m3 | kgf/mm2 | kgf/mm2 | kgf/mm2 | kgf/mm2 | HV | |||
C// | C⊥ | |||||||||||
Neodymium | 35 | 6.5X10^6 | -1.5X10^6 | 1.05 | 0.12 | 1.3X10^4 | 7.5 | 25 | 110 | 7.5 | 1.7X10^4 | 600 |
Samarium cobalt |
YXG28 | 8X10^6 | 10X10^6 | 1.05 | 0.1 | 0.9X10^4 | 8.5 | 15 | 80 | 4 | 1.2X10^4 | 550 |
Ferrite | Y30H-1 | 15X10^6 | 10X10^6 | 1.15 | 0.2 | >10^2 | 5.0 | 7 | 70 | 4 | 1.2X10^4 | 530 |
Alnico | LNG40 | 10X10^6 | -10X10^6 | 3.6 | - | 5X10^4 | 7.3 | 7.5 | 300 | 4 | 2X10^4 | 650 |