Processo di produzione dei magneti
1.Pesatura delle materie prime
Metalli in terre rare, ferro, cobalto e altri elementi aggiunti che sono stati composti a formare una lega per la produzione vengono pesati. Queste materie prime vengono messe in un forno di fusione sottovuoto.
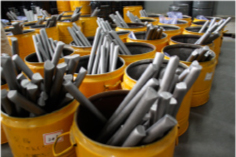
2.Fusione
Alle materie prime situate nel forno di fusione sottovuoto viene applicata un’elevata frequenza per farle fondere. Con l’aumento della temperatura la lega diventa omogenea, dopodiché viene versata in stampi per formare dei lingotti.
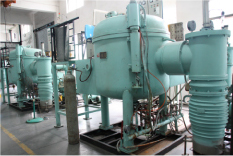
3.Polverizzazione
Dopo diversi passaggi i lingotti vengono polverizzati fino a diventare delle particelle molto sottili di pochi micron di diametro medio per particella. Il processo di polverizzazione viene eseguito in un ambiente protetto di argon o azoto per evitare l’ossidazione delle particelle.
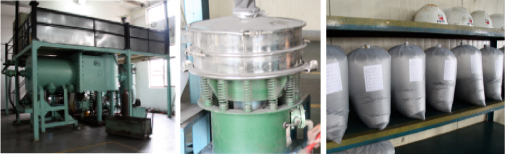
4.Stampaggio nel campo magnetico
La polvere magnetica a cui è stato applicato un campo magnetico viene pressata in uno stampo. Il risultato che si ottiene è che l’orientamento del cristallo delle particelle segue la direzione del campo magnetico esterno migliorando così la direzione di orientamento delle proprietà magnetiche.
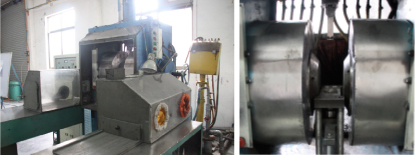
5.Sinterizzazione e trattamento termico
Il composto pressato subisce una sinterizzazione e un trattamento termico nel forno di fusione sottovuoto. Il composto viene poi “cotto” fino a raggiungere un livello di concentrazione che si avvicina ad una densità reale. A questo punto, le dimensioni del composto sinterizzato vengono compattate fino ad un 70-80% rispetto al composto pressato e il volume è di circa la metà. Il trattamento termico dopo la sinterizzazione fa sì che la struttura metallica della lega magnetica venga regolarizzata.
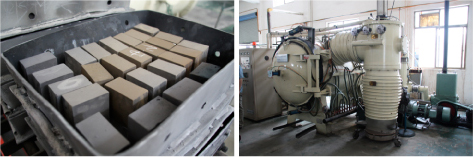
6.Ispezione delle caratteristiche magnetiche
Le caratteristiche magnetiche di base del magnete si ottengono dopo che il processo di sinterizzazione e del trattamento termico è completato. Le caratteristiche magnetiche del magnete quali la densità residua del flusso magnetico, la coercività, e l’energia massima prodotta vengono misurate e solamente i magneti che superano il test vengono inviati ai prossimi passaggi di lavorazione e assemblaggio.
7.Lavorazione
Durante la sinterizzazione, i magneti in terre rare subiscono un restringimento di grande quantità e, per rimuovere lo strato di ossidazione che si è formato sulla superficie, il magnete viene sottoposto ad un trattamento di lucidatura o taglio prima di arrivare a raggiungere le dimensioni desiderate.
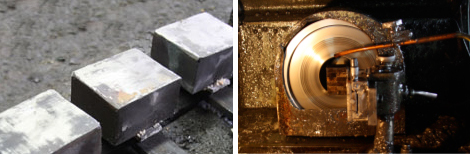
8.Trattamento della superficie
I magneti vengono sottoposti ad un trattamento della superficie in base all’ambiente in cui verranno utilizzati. Generalmente i magneti al neodimio arrugginiscono facilmente e quindi vengono sottoposti ad una placcatura o rivestimento in nichel. Al contrario, i magneti in samario-cobalto, dalle ottime proprietà anticorrosive, generalmente non sono soggetti a nessun trattamento di superficie.
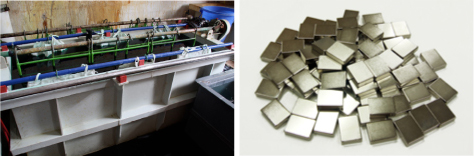
9.Ispezione visiva dell’aspetto
Dopo i passaggi della lavorazione e del trattamento della superficie si effettua l’ispezione visiva dell’aspetto e delle dimensioni. Inoltre, attraverso dei test si verificano le caratteristiche magnetiche e anticorrosive in base ai dati tecnici del prodotto.
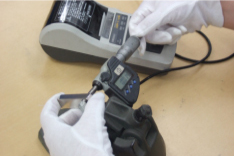
10.Magnetizzazione
Si esegue la magnetizzazione usando un campo magnetico statico o un campo magnetico pulsato.
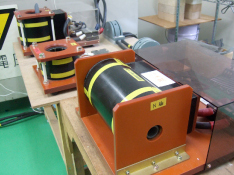
11.Imballo e spedizione
I magneti che hanno superato il test dell’ispezione vengono imballati e quindi spediti.
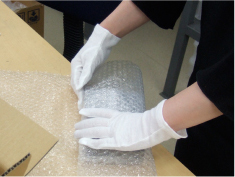